An inventory management system is the collection of items or materials that a business intends to sell to customers for profit. A good inventory management system is a critical element of the supply chain, an inventory management system facilitates the tracking of inventory from the time of manufacture to the warehouse, and from the warehouse to the point of sale. The goal of inventory management is to have the right products in the right place at the right time. This requires inventory visibility: knowing when to order, how much to order, and where to store inventory.
However, only 43 percent of small businesses track and manage their inventory management system well due to, among other circumstances, lack of methodologies, little knowledge about the importance of the subject or lack of adequate tools to do so; which can irreversibly damage the business.
Considering the value of an inventory management system in the growth and survival of companies, I want to dedicate this article to point out what is an inventory management system, what is its objective, the importance of the subject for companies and the different types of inventory management system that exist to automate this work.
What is an Inventory Management System?
Inventory is one of the most important assets to a company's business operations, especially for growing companies, as full knowledge of stock levels ensures that businesses run efficiently and can plan their finances. Companies that use an inventory management system effectively are destined for success.
Through inventory management, the company tracks and controls warehouses and inventories as they are purchased, manufactured, stored and used. This means that warehouse management directs the entire flow of goods, from purchase to sale, ensuring the organization always has the right quantities of the right item, in the right place, at the right time.
Inventory management is the process of coordinating the flow of goods in a company in a continuous cycle of ordering, storing, producing, selling and replenishing goods. Inventory management systems generally work at two levels: aggregate inventory management and storage location and item-level inventory management. In determining your inventory strategy, companies make trade-offs between minimizing the amount of cash tied up in inventory or holding more inventory to maximize customer service or production efficiency.
Inventory strategy involves managing inventory at the item level through policies, such as safety stocks (described below), and inventory controls through policies, such as ABC classification to prioritize replenishment rates, that take item-level attributes, such as consumption value, lot size, and order lead times.
Inventory can be broadly classified into three categories: raw materials/components, work-in-process, and finished goods. Manufacturing companies purchase raw materials or components, store them until they are ready for production and transform them into finished goods. Non-manufacturing companies, such as wholesale and retail distributors, store finished products for sale to final consumers (learn more about Dynamics 365 for Manufacturing here).
All businesses must achieve a balance between inventory levels and demand because inventory consumes a company's cash and incurs carrying costs. Regardless of the type of business, companies must maintain tight control over inventory to conserve cash while ensuring they have enough items to meet production schedules or anticipated customer demand and actual orders.
Importance of an Inventory Management System in Businesses
A proper inventory management system is critical to the success of any business and to the efficient management of the company's processes and operations.
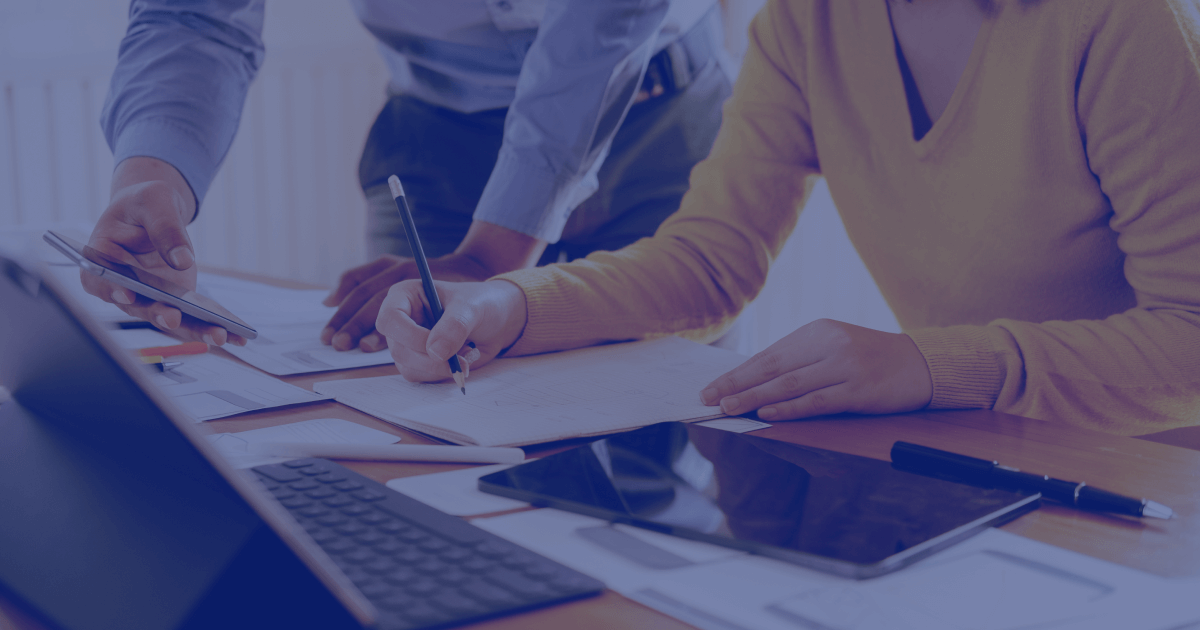
Having control of warehouses and inventories is one of the main ways in which a company can maximize its potential sales, because if it does not maintain an adequate level of stock in its warehouse, it can lose customers. Conversely, if you have too much, you run the risk of your inventory becoming obsolete or deteriorating. Having to discard products because they are spoiled or perished becomes costly for companies, especially if it happens frequently.
In this way, we can say that inventory management enables businesses to fulfill purchase orders on time and accurately.
Types of Inventory Management Systems
With the help of an inventory management system, companies can automate the process of ordering, storing and optimizing their products from one place, leaving behind isolated applications and paper records.
There are several types of inventory management systems that can be used by small and medium-sized businesses (SMBs).
Just-In-Time (JIT) Inventory System
This is an inventory management system for ordering raw materials or goods and receiving them only when they are needed to keep the production process running to meet actual customer demand. In other words, excess stock is not requested and must arrive just in time for manufacturers to use in the production process.
ABC Analysis System
Also known as ABC Classification, this type of system allows businesses to distinguish the products in their inventory stock and focus on managing them based on their value. Its main objective is to help make the most of the minimum investment, without wasting resources or inventory. The system classifies stock into three categories: A, B and C, based on revenue.
Perpetual inventory systems
This type of system tracks inventory on an ongoing basis, meaning that updates are made automatically when new inventory is acquired. It works best when used with warehouse inventory, a database of inventory quantities and garbage can locations updated in real time.
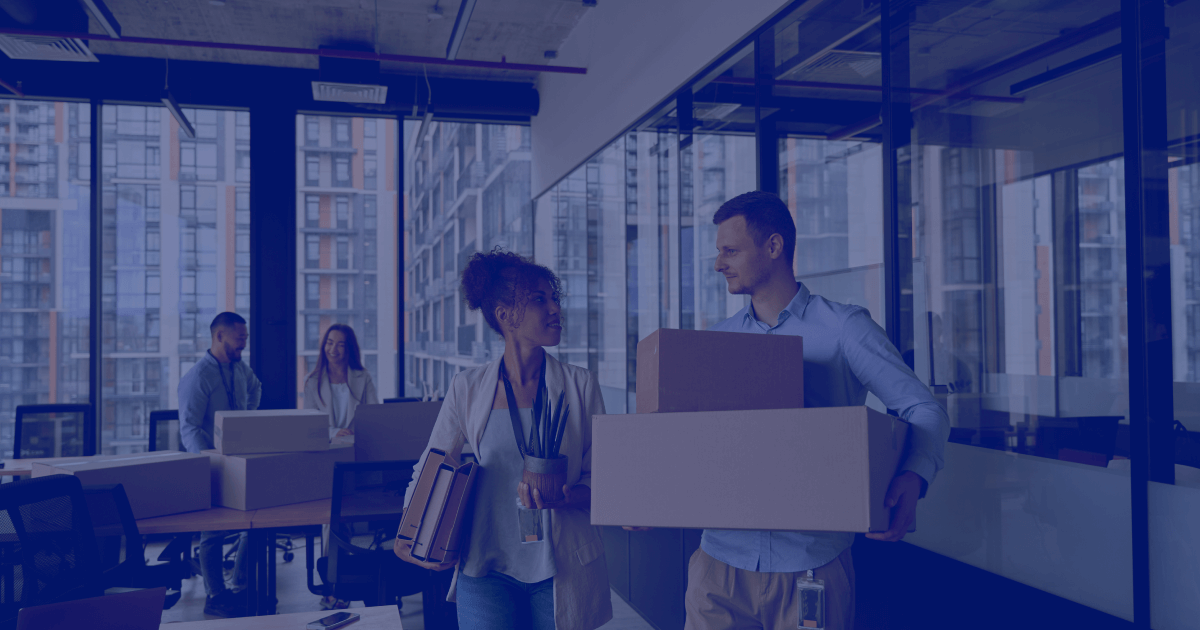
Periodic inventory system
Does not track inventory daily but allows companies to know beginning and ending inventory levels over a certain period. To use these systems, it is necessary to use software, usually an inventory management system.
Bar code inventory system
They use barcode numbers to identify each product being sold. The numbers can represent different data related to the item, including supplier and manufacturer, product location, weight, quantity of each item in stock, etc.
Radio frequency identification systems
These systems use both active and passive technology to manage inventory movements. Active RFID technology uses fixed tag readers throughout the warehouse. RFID tags are passed through the reader and the movement is recorded in the inventory management software.
Benefits of an Inventory Management System
A modern ERP system provides information on stock levels, inventory on the way and current inventory status, which will turn your inventory management into a competitive advantage for your business.
Inventory management is complex and varies by industry, your role within the company and the type of item being managed. Deciding how to plan and manage inventory is a collaborative effort fraught with risk and reward.
No two companies are alike. Depending on the business model, companies use several different methods to manage inventory. Inventory costs the company money, but it may be necessary to hold more safety stock to maintain superior service levels to avoid stock-outs and maximize operational efficiency. Manufacturers with expensive machine and people operations sometimes hold excess inventory to avoid shutting down these operations due to stock-outs, which would cost the company more money.
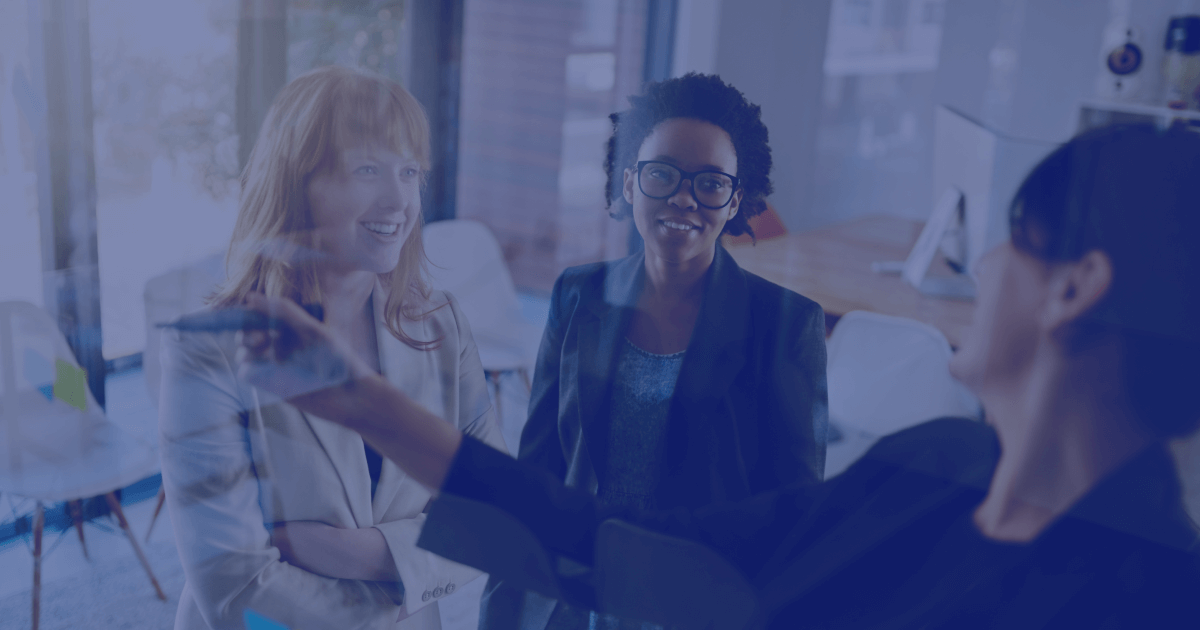
Almost all companies maintain a safety stock inventory to protect against unexpected changes in supply and demand. In this way, inventory functions as a hedge against the unexpected and as a buffer against production stoppages. Safety inventory represents a trade-off between service or fulfillment rates (the percentage of customer orders that a company can ship immediately from inventory) and the additional cost of ordering and holding more inventory. The consequence of not having enough inventory is stock-outs, which can be detrimental to a company, especially if customers have alternatives, such as e-commerce-based companies where quick fulfillment is expected. Stock-outs represent lost revenue and can negatively affect customer loyalty.
Manufacturers often establish inventory controls, such as minimum and maximum stock levels and reorder points, within their ERP systems. Distributors set reorder points on a decentralized basis, allowing each distribution center to determine its inventory levels based on local factors or demand-based methods. Local factors may include SKU-level demand, lead times or seasonal patterns. Demand-based methods may include point-of-sale data from retail customers. Many purchasing organizations factor price discounts into the purchasing strategy and may purchase more supplies than necessary to obtain favorable price points.
Best Practices for Inventory Management Systems
The goal of inventory management is to help warehouse managers keep track of the stock levels of their products, giving full transparency and visibility into the supply chain.
When done efficiently, inventory management can become the cornerstone of business success. With a strategy that optimizes the warehouse and inventory control process, and provides immediate access to real-time data on inventory conditions and levels, companies can achieve important objectives, including:
Accurate fulfillment of purchase orders or purchase orders, avoiding poorly executed orders, high return volumes and loss of customer base.
Increased customer satisfaction, as there is no worse experience for customers than having their orders delayed or damaged. In addition, good inventory management streamlines the order fulfillment process, allowing orders to be shipped to customers faster.
More efficient inventory planning, because detailed inventory management helps evaluate which products are needed, allowing warehouse managers to update inventory only when necessary.
Reduced costs, because by keeping control of inventory, costs for the purchase of more material for production are reduced.
Examples of Inventory Management Systems
While inventory management is common in most industries, there are industries with unique requirements that warrant specialized systems. Notable examples are food service (restaurants) and retail.
Retail inventory management
Today, retailers must offer customers highly flexible purchasing options for products offered through different channels. Intense competition from large e-commerce providers and demanding customers have forced retailers to operate a blended business model, combining physical stores and online shopping experiences, known as omnichannel retailing.
Omnichannel gives shoppers flexible options, such as ordering in-store, shipping to home, buying online, returning in-store, or shipping from a distributor to a store for pickup. The goal is to provide an excellent customer experience from start to finish, which could mean the difference between success and failure.
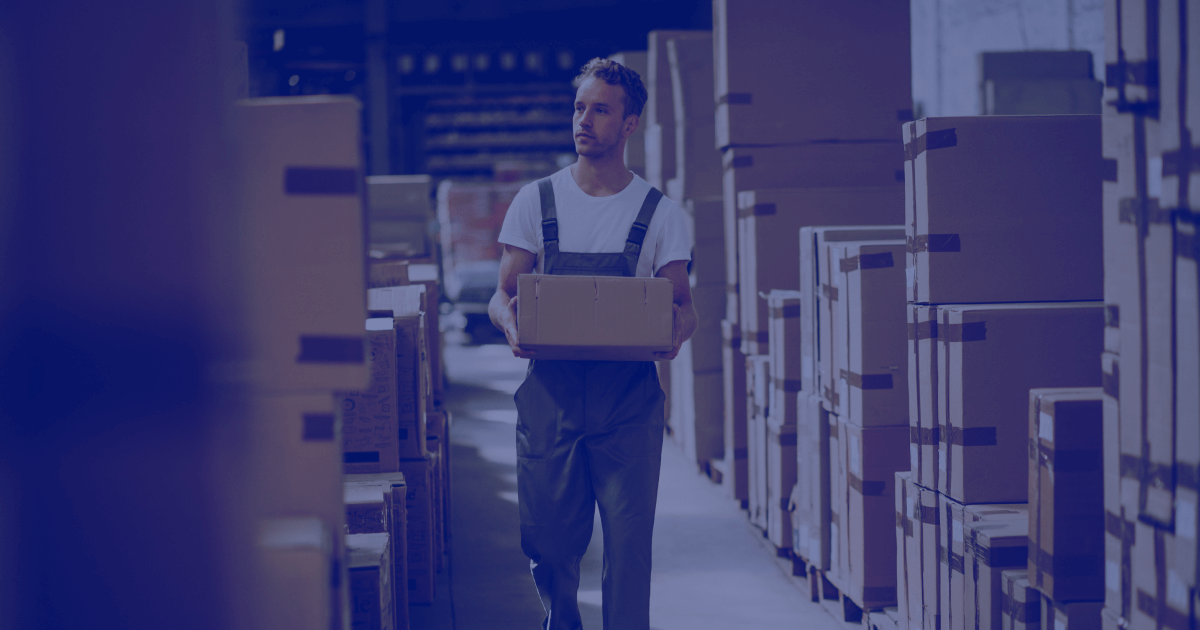
To deliver the best omnichannel customer experience, retailers must have real-time visibility into their on-hand inventory to ensure the customer's shopping experience translates into orders. Stock-outs not only prevent specific orders from being filled, but frustrated customers are also very likely to look for similar items in-store or on a competitor's website. Loyalty is fleeting and brand switching is common. Lost customers may never return and affect potential future sales.
As a result, retailers must manage inventory very carefully to fine-tune the fine line between having enough inventory to fill the highest percentage of their customers' orders and not having too much, which reduces their cash flow and risks having leftover stock at the end of a buying season that cannot be sold. Retail inventory management software (combined with order management systems) allows retailers to react quickly to changes in buying behavior and adjust their channel strategies and inventory levels.
Restaurant inventory management systems
Restaurant inventory management is unique in that it must provide real-time ingredient tracking because many ingredients are fresh, have a short shelf life and are carefully tracked to consumption. The system must also carefully monitor stock levels, trigger replenishment orders, record new inventory receipts, and help manage menu costs.
Fresh ingredient management has inherent challenges in helping managers closely monitor shelf life to avoid spoilage. At best, spoilage results in a loss of money, while at worst, it can cause food poisoning and trigger action by health authorities.
Inventory management systems’ software can help restaurants manage their challenges. By automatically connecting sales with inventory levels, restaurants can have a complete view of orders, consumption, know ingredient stocks, avoid spoilage and manage their margins. Inventory management systems’ software also reduces time spent on administrative tasks by sending alerts to managers about potential shelf-life expirations, automating reordering when items exceed spoilage dates or fall below established replenishment levels.
Inventory management system software
Modern cloud-based inventory management systems provide comprehensive materials management capabilities that effectively manage the flow of goods across your enterprise and global supply network. Together with warehouse management systems, they provide accurate and timely visibility into inventory levels, replenishment plans and order fulfillment rates, all of which impact customer satisfaction. Combined with supply chain planning systems, they take the guesswork out of inventory management systems by matching demand with supply through optimizing inventory levels, increasing order fulfillment rates, ensuring scheduled production runs, and improving working capital utilization.
Inventory management systems and supply chain management.
Inventory management is a critical component of supply chain management meaning the movement of goods, whether delivering raw materials and subcomponents to manufacturers or fulfilling orders for finished goods. Both help companies reduce costs, improve cash flow and increase profit margins.
Inventory Visibility
A key benefit of a modern cloud inventory management system is the ability to provide real-time visibility into inventory at multiple nodes in the supply chain, such as production facilities, suppliers, goods-in-transit and distribution centers. This gives decision makers the information they need to maintain customer satisfaction. This is particularly critical for companies with extended supply networks, variable demand and intense competition.
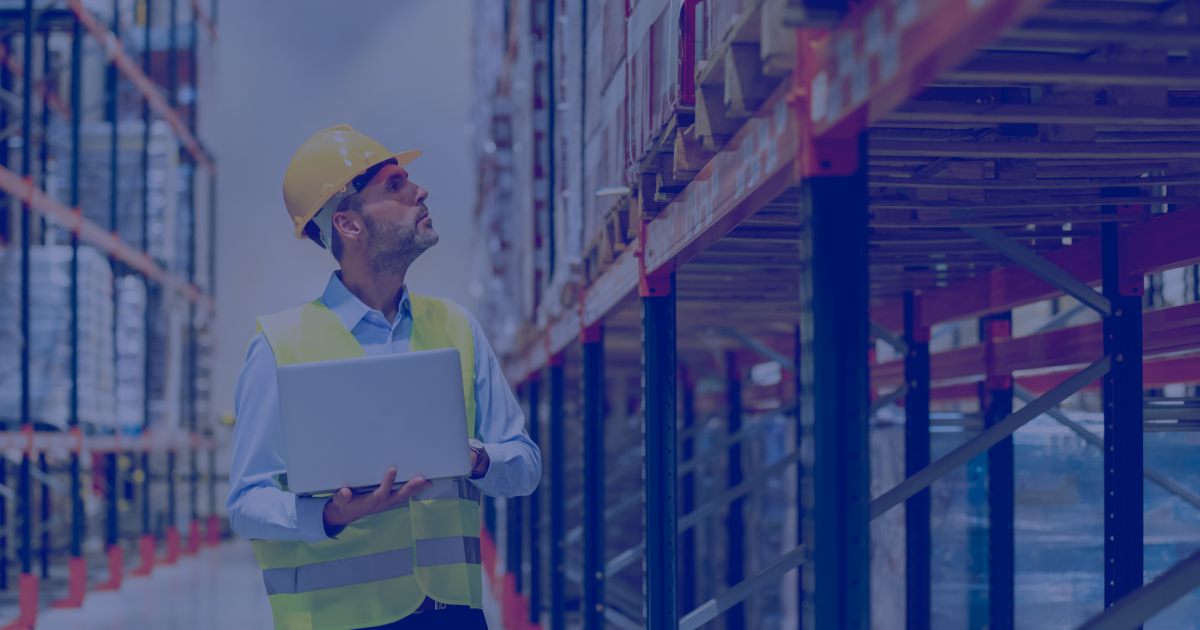
A real-time view of stock levels and their location helps them better manage production schedules and the processing of customer orders. For example, if a delivery is delayed due to transportation problems, managers can cover the temporary shortfall by moving stock from one distribution center to another where higher demand levels justify more inventory.
Combined with supply chain planning software, having real-time data on order volumes helps planners determine how much of a particular item they need, where they need to place it, and how often they need to replenish in order to meet actual and forecasted demand and production levels.
Integrated supply chain planning
Complex supply chains challenge companies to align supply with demand and determine inventory levels more accurately. Sophisticated demand planning solutions can help use sophisticated algorithms that incorporate multiple scenarios, including item and location combinations, as well as inventory policies to generate the optimal demand plan. What-if scenarios play a vital role in ensuring that planned inventory levels are sufficient to meet customer demand, avoid stock-outs and ensure resilience.
Supplier management to optimize your inventory management system
Choosing the right suppliers is the responsibility of the purchasing division. Suppliers can have a significant impact on inventory. For example, achieving just-in-time availability depends on having reliable and qualified suppliers who can meet specific delivery deadlines. If they miss scheduled ship dates, production and customer orders can be delayed, resulting in decreased customer satisfaction.
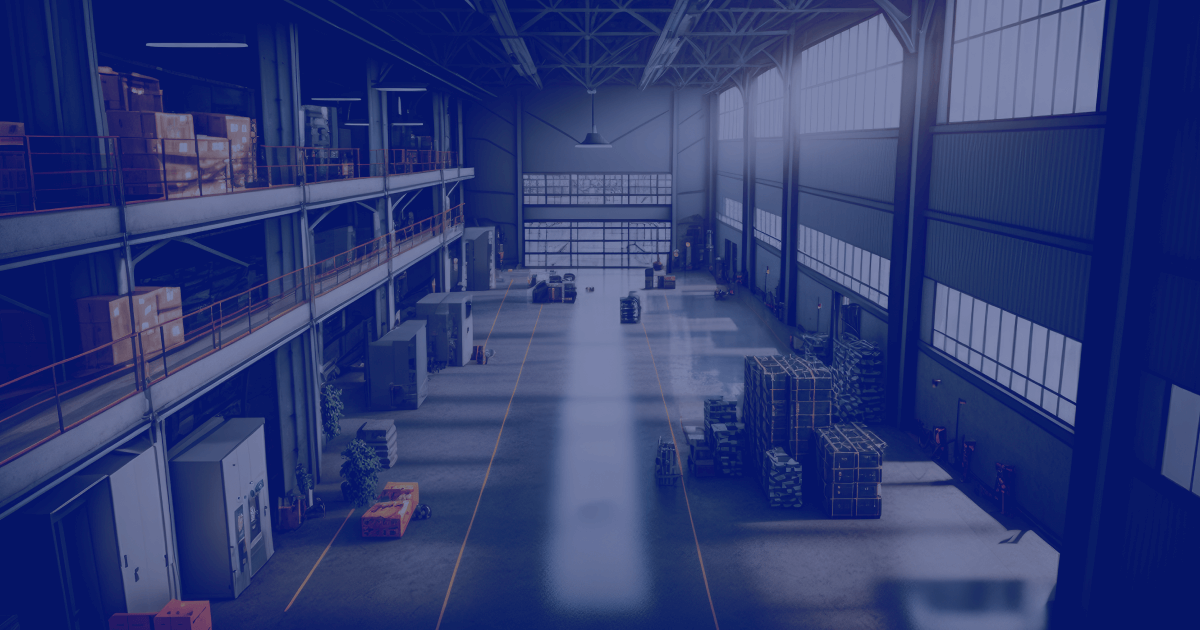
The net requirements plan incorporated through supply planning into the demand plan must be able to support the complexity of global supply chains to determine raw materials and inventory requirements for production. Finally, planning systems help determine inventory policies to establish safety inventory levels (excess inventory used as a buffer against supply and demand uncertainty) essentially taking the guesswork out of inventory decisions and their potential negative impact on cash flow.
Integrated business planning combines statistical forecasts with actual demand signals to provide up-to-date forecasts and inventory levels that meet desired or desired customer service levels. Helps manage uncertainty in demand and supplier lead times. Replenishment orders are generated whenever an inventory item falls below a minimum threshold. These orders incorporate estimated lead times to ensure adequate stock levels. Depending on the specified inventory policy, the replenishment order can be a fixed order quantity or a calculated quantity, calculated as a difference between the maximum threshold and the inventory item, and can be adjusted for minimum order quantities.
Inventory management system in the cloud: where are you on your journey?
If you're ready to learn more about modern inventory management, a good place to start is xplusglobal.com.